DBP, LBP seek loan payment
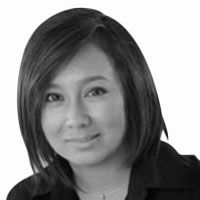
Two government-owned banks have demanded the immediate payment of loans obtained by a huge shipping company based in Cebu.
According to documents obtained by The STAR, The Land Bank of the Philippines (LBP) and the Development Bank of the Philippines (DBP) are seeking the recovery of nearly P5 billion from Cebu-based Asian Marine Transport Corp. (AMTC) which obtained the loans as early as 2009.
According to the company’s website, AMTC provides end-to-end transport and logistics services as well as shipping services for inter-island passengers and cargoes, being the largest ship-tonnage owner and operator in the Philippines, serving 32 ports of call.
Last Dec. 6, DBP sent AMTC a final demand to settle its past due loan obligation amounting to P1.479 billion as of Oct. 31, 2024. The loan has been due since Jan. 31, 2019. Should DBP fail to make payment, the bank said it would be constrained to initiate foreclosure proceedings on the mortgaged properties and to file a criminal and/or civil case for collection with damages.
Documents showed that at least six ships of AMTC were used as collateral to secure the loans.
In one letter sent to DBP, the company said it did not have the cash to settle its past due obligations with the bank, but reiterated its appeal to “mutually find ways that will allow us to make payments to the extent that we can without crippling or totally stopping the operations of the company.”
For its part, LBP sent a separate demand to AMTC on Dec. 13, 2024 to pay its loan obligation to the bank, the outstanding principal of which has reached P3.413 billion exclusive of interests, penalty charges and advances.
AMTC’s account with LBP includes a short-term loan line and seven term loans, most of which were taken from UCPB which has been folded into the state lender. LBP noted that AMTC loans had been restructured on Dec. 23, 2019 and Sept. 30, 2022. To secure the loans, AMTC used as collateral 12 ships it uses for its operations, among other assets.
Wait-and-see
The local cement industry has adopted a wait-and-see stance before moving on with its expansion and modernization programs.
This attitude is highly justified.
Of the industry’s roughly 52 million installed capacity, capacity utilization is around 70 to 80 percent, translating to an availability of about 36 million tons of locally produced cement. Local demand for cement, meanwhile, as of last year was around 35 million tons which means that Philippine cement manufacturers are more than capable of meeting demand.
Unfortunately, at least for the past six years, cement imports have been on a meteoric rise. Last year, imports reached about 7.6 million tons. Add that to the 36 million tons of domestically produced cement or a total supply of around 44 million tons. With local demand at 35 million tons, then clearly there is a glut or excessive supply of cement in the country of about nine million tons.
About 80 to 85 percent of imports are from local companies and traders, including Philcement which is said to have imported two million tons, Fortem Cement Corp., Davao Trading and Cohaco Merchandising.
We don’t need to import cement.
Vietnam is the largest exporter of cement to the Philippines, accounting for around 97 percent of cement being brought into the country. In fact, the Philippines is Vietnam’s biggest market for its cement. Vietnam is said to have an installed capacity of 150 million tons while its local demand is only 60 million tons. Their manufacturers, many of which are state-owned companies, have to get rid of that oversupply one way or the other. And that is where dumping comes in.
The Philippine government has imposed definitive anti-dumping duties on several Vietnamese exporters to the Philippines beginning March of last year ranging from 2.33 percent to 23.33 percent depending on the exporting company. These are imposed on ordinary Portland Cement Type 1 and Blended Cement Type 1P and would remain in effect for five years.
Late last year, there were separate petitions to the Tariff Commission from the Department of Trade and Industry and some of the country’s biggest cement manufacturers to expand the anti-dumping duties to additional cement types and manufacturers, in particular Blended Cement Type 1T.
Unfortunately, these anti-dumping duties are imposed only on a number of Vietnamese exporters who supply about 20 percent of cement being exported to the Philippines.
Anti-dumping duties are imposed on top of the regular import duties when these imported products are found to be the subject of dumping, meaning it is being sold at a price lower than their normal market value, causing harm to domestic producers in the importing country. The imposition is done after the Tariff Commission determines that there is proof of dumping and substantial injury to the domestic industry and after determination that the anti-dumping measure complies with World Trade Organization Rules. Dumping is considered as an unfair trade practice.
The imposition of anti-dumping duties on about 20 percent of the cement being brought into the country, however, has not and will not completely address the burgeoning problem of oversupply.
It is for this reason that our DTI has initiated a preliminary safeguard measures investigation on the importation of cement not only in Vietnam but also other countries as well. This could result in the imposition of provisional safeguard duties for a period of 200 days pending further investigation by the Tariff Commission for the slapping of definitive safeguard duties on top of the regular import duties and anti-dumping duties.
According to the DTI, cement imports increased by 10 percent in 2020, by 17 percent in 2021, by five percent in 2023, and by 52 percent during the first half of 2024. From cement imports of 5.33 million tons in 2019, this has gone up to over seven million tons.
Unlike dumping duties, safeguard measures are imposed if the volume of imports of a product are found to be of such quantity that it becomes injurious or threatens to injure the domestic industry for the like product.
While the situation may appear to be beneficial for those using cement in the short run, the reality is that not only are we getting imported cement whose quality is questionable; the ramifications of losing a vital industry such as cement manufacturing are huge, not only in terms of loss of direct and indirect jobs, loss of taxes paid by cement manufacturers and other allied and industries that indirectly rely on it, among others. Because of the oversupply situation, capacity utilization of local cement makers is said to be down to 60 percent, which means less work and pay for many of their workers.
It would also be good if both our national and local governments as well as their contractors start buying only local cement. After all, they account for around 40 percent of demand for cement. The Tatak Pinoy Act after all mandates the government to prioritize locally produced goods and services in its procurement activities. Let’s hope that the rules of the newly enacted law will include government contractors as well.
For comments, email at maryannreyesphilstar@gmail.com
- Latest
- Trending